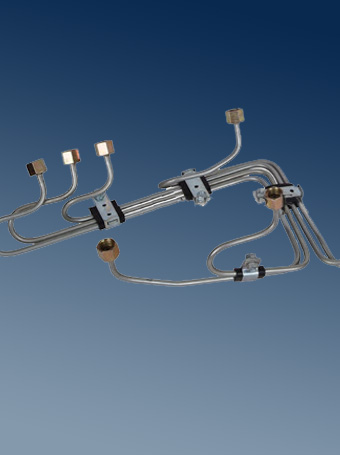
Fuel injection pipes
The Fuel injection pipes exported by us are made from Seamless Tubes and Forged Nuts manufactured by our parent company M/S Gandhi Special Tubes Ltd.
The seamless tubes are scale free, bright, soft, annealed tubes with a very clean bore (mirror finish) and having surface roughness value below 2 microns Ra.
These pipes are fully Fabricated as per O.E Specifications & Designs, i.e. Pipes are Forged, and fitted with forged Nuts and bending is done as per O.E drawings or samples.
Fuel Injection lines for
- DIN 73000 ( ST 30 Al )
- DIN 73000 ( ST 52.4 )
- ISO 8535-1
- SAE J1958
Quality & Inspection
Strict measures are taken to ensure Scale free and bright tubes with high degree of internal cleanliness conducting following tests:
- Salt spray Test
- Tensile Test
- Hydrostatic pressure Test
- Eddy Current Test
- Flattening, Flaring, Bending Test
- Surface roughness Test
- Hardness Test
- Burst Test
- Chemical Laboratory
- Metallurgical & Stereo Microscopes
- Various gauges for Dimension measurements
Product Highlights & Strengths
- Scale free bright tubes as annealed/normalized in bright annealing furnace under reducing atmosphere
- Tubes are manufactured out of fully Aluminum killed steel only to avoid problem of ageing which can lead to embrittlement & cracks.
- Surface roughness will be below 2 Microns Ra value as per O.E.M specification

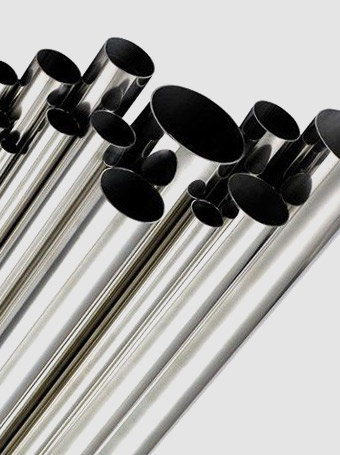
Cold Drawn Bright Anealed Seamless Tubes
Cold Drawn Bright Anealed Seamless Tubes exported by us are manufactured by our parent company; M/S. Gandhi Special Tubes Ltd.
Gandhi Special Tubes Limited (ISO/TS 16949:2009 and ISO 9001:2008) set up its plant in technical collaboration with BENTELER STAHL/ROHR GMBH & CO.AG of Germany, and is engaged in manufacturing of Cold Drawn Seamless Tubes.
- Outer Diameter: From 3.0 mm up to 75 mm.
- Wall Thickness: From 0.5 mm up to 7.5 mm.
- Hydraulic Tubes.
- High Pressure Diesel Fuel Injection Tubes.
- Tubes for General Engineering Applications.
- DIN 2391
- DIN 2445
- DIN 17175
- EN 10305-1 & EN10305-4
- EN 10216-2
- BS 980
- BS 3059
- IS 3601
- IS 3074
- SEE J 524
- SAE J 1958
- SA 179
- SA 210
- SA 334
Strict measures are taken to ensure Scale free and bright tubes with high degree of internal cleanliness conducting following tests:
- Tensile Test
- Hydrostatic pressure Test.
- Eddy Current Test
- Flattening, Flaring, Bending Test
- Surface roughness Test
- Hardness Test
- Burst Test
- Salt spray Test to test Phosphating
- Chemical Composition
- Metallurgical & Stereo Microscopy
- Dimensional Checks
- Scale free bright tubes as annealed/normalized in bright annealing furnace under reducing atmosphere
- Tubes are manufactured out of fully Aluminum killed steel only to avoid problem of ageing which can lead to embrittlement & cracks.
- Surface roughness will be below 2 Microns Ra value for fuel injection Tubes
- Uniformly annealed soft tubes, suitable for proper ferrule biting.
- Reliable source of raw material.
- Tubes can be supplied with even closer dimensional tolerance than permitted by various codes/specifications, subject to prior agreement.
- Quality Assurance System as per ISO 9002.

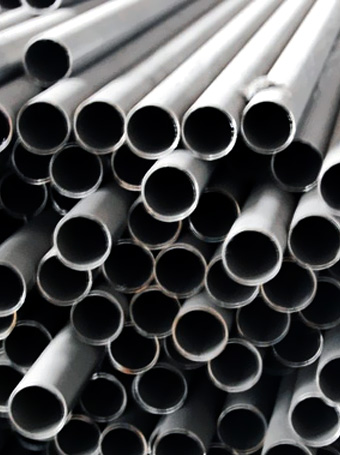
Precision Electric Resistance Welded Tubes
PERW (Precision Electric Resistance Welded) Tubes exported by us are manufactured by our parent company, M/S. Gandhi Special Tubes Limited (ISO/TS 16949:2009 and ISO 9001:2008) set up its plant in technical collaboration with BENTELER STAHL/ROHR GMBH & CO.AG of Germany. The project involves manufacturing of small diameter precision welded steel tubes.
- Outer Diameter: From 3.1 mm up to 12.7 mm.
- Wall Thickness: From 0.5 mm up to 1.5mm.
(Tubes can be supplied in straight lengths or in coil form.)
- Condensers for refrigerators
- Compressor tubes
- Tubes for automobile applications such as fuel lines, oil lines, air brake lines
- General Engineering applications.
- DIN 2393
- DIN 2394
- EN 10305-2
- SAEJ 526
- SAEJ 356 etc or equivalent
Strict measures are taken to ensure Scale free and bright tubes with high degree of internal cleanliness conducting following tests:
- Bubble Test to check Leakages with dry nitrogen under water @ 70 bar pressure.
- Tensile Test
- Flattening, Flaring, Bending Test
- Eddy Current Test
- Micro hardness Test
- Chemical Composition
- Metallurgical & stereo Microscopy
- Dimensional checks
The precision welded steel tubes are manufactured using the latest and most advanced technology. Raw material is DD/EDD grade low carbon steel CRCA coils. The process involves continuous Forming, Direct Current Welding, and Sizing by passing through a set of stretch reducing rolls and thereafter followed by bright annealing in continuous roller hearth Furnace under reducing atmosphere. The resultant tubes are Soft, Scale free and Bright having excellent physical properties.
The tubes are pressure tested at @ 70 kg/cm2 pressure with dry nitrogen under water before straightening and finishing operations. The continuous manufacturing process enables supply of the tubes in straight lengths & coils up to 1000 meters.

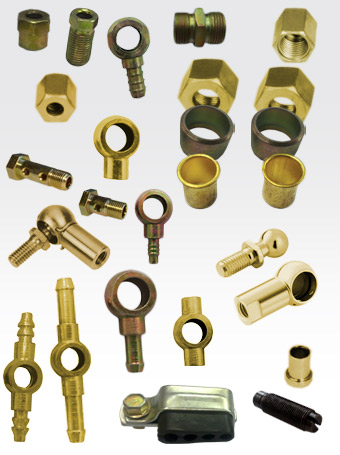
Tube Fittings & accessories
Tube Fittings & accessories Exported by us are cold forged. The raw material used for manufacturing these tube fittings are as per International Standard.
Application
- End connections for High pressure Fuel injection Tube Assemblies.
- End Connections for Nylon and other Automobile Tubing's Hydraulic Fittings
Product Highlights & Strengths
- Stringent quality control is maintained during and after manufacturing process to ensure that the products are as per O.E.M standards and specifications.
- High Degree of Reliability ensuring Zero Failures on account of Cracked nuts
- Greater Shear Strength than Machined Nuts
- Excellent Surface Finish which not only gives better looks to the nuts but improves product life
